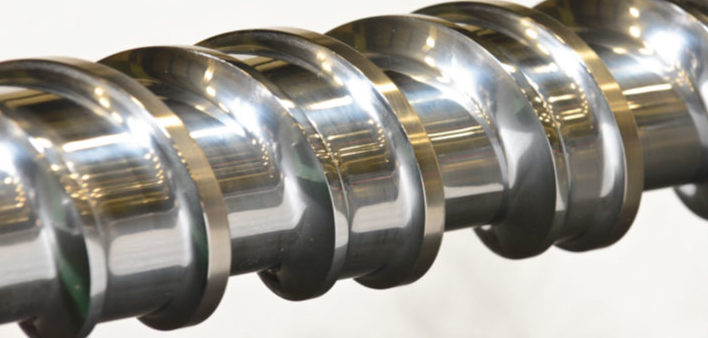
Five Things Some Feed Screw Suppliers May Not Want You to Know
- Where was the screw manufactured? There are numerous brokers with great looking web sites and search engine optimization that make a processor think they are dealing with a reputable feed screw design and manufacturing house. In order to receive a quality product, processors should ask questions to include: a) Country of origin – where the screw was manufactured b) Country of origin of the base steel of the screw (United States, Eastern Europe, China, etc.), c) Hard facing OEM or generic equivalent, d) Where the screw was coated i.e., chromed, carbide coated, nitride hardened, etc. Brokers likely will not know the answers to many of these questions; however, screw manufacturers will know the answers to all of these questions. Processors should be aware that not all material sources or coating vendors meet the same standards.
- How did the supplier arrive at the screw design they are providing? Many screw designs may sound custom, but are, in fact, off the shelf versions. A “one size fits all” mentality does not optimize for your specific process, materials, L/D, or other factors. And what about custom mixing geometry such as distributive mixing melting designs? Why aren’t those designs offered? Only a few custom screw manufacturers will offer this alternative geometry because only a few understand how to design and implement it, and even less understand how to manufacture this geometry.
- Delivery – how can it be this fast? If it’s available quickly, it’s probably a GP–General Purpose–design, also described as “Generally Poor” for many processes. Something off the shelf may get you up and running sooner, but the processor must determine if getting something in 3 weeks or sooner that will process for 4 – 7 years is really the best value for the long term.
- Quality matters to consider? Is the hard facing applied full flight width? Many screws are “welded in the groove” with base material on the sides of the tips of the flights. That method, while cheaper to manufacture, will wear faster than a full flight width hard faced screw. Other factors to consider include concentricity (think a circle turning inside a circle and how that might affect surging or side loading), hardness testing of hard facing (was the hard facing over diluted with base screw material during application resulting in relatively soft hard facing, for example), and straightening during the manufacturing process. If a screw was ground straight, it may not be concentric. These factors can all impact wear and processing.
- Price vs. value proposition? The value proposition is always a consideration. Price is what you pay, value is what you get.
By Mike Mieduch – Sales Manager at Glycon Corporation in Tecumseh Michigan. Glycon Corporation has been designing and manufacturing feed screws for the plastics industry for 38 years. Mike has been actively employed in the plastics industry for 41 years.